SLS 3D Printing Advantages
-
By
Marie-Christine Flibotte
April 4 2022
-
Applications industrielles
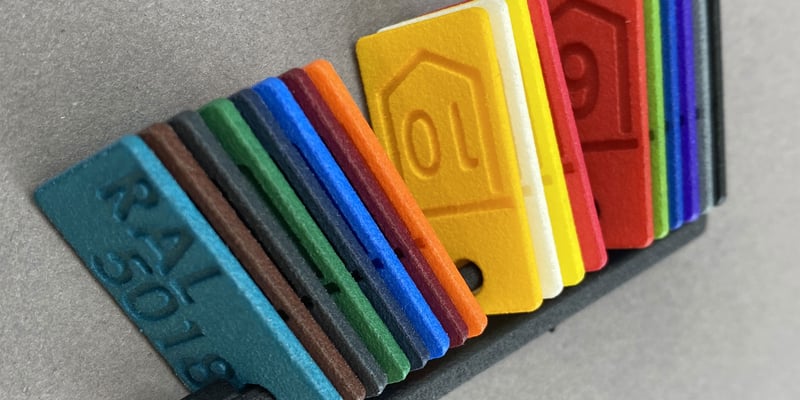
Solaxis Ingenious Manufacturing are leaders in additive manufacturing of thermoplastics. Several months ago, they acquired industrial SLS (Selective Laser Sintering) equipment. But what are the advantages of using industrial 3D printing technology of thermoplastic powder?
COST OPTIMIZATION
In general, SLS 3D printing has many advantages. This technology optimizes the impressions and allows the production of several parts in the same production batch. Its “nesting” technique is advantageous because it directly impacts productivity and production time (+/- 7 business days), while implicitly impacting production and parts costs. This optimizes series production and considerably reduces the cost per part, especially in the case of smaller parts.
INCREASED PRODUCTIVITY AND PRODUCTION RATE
By using this technology, Solaxis Ingenious Manufacturing can produce orders of small and medium series that could reach up to 20 000 parts per month. The SLS manufacturing envelope is 15x15x17 inches, which is relatively large on the SLS market.
DURABLE PARTS
For certain mechanical property values, the new technology at Solaxis allows them to reach superior properties compared to other materials on the industrial 3D printing market, at a lower cost. For example, the elongation at break can reach over 30% and the ultimate tensile strength is also very high. Furthermore, SLS parts’ isotropic properties have many advantages in cases where the parts are solicited mechanically.
If we take the example of nylon SLS parts, they have a density close to 100% and mechanical characteristics close to those that can be reached using traditional manufacturing methods.
HIGH-RESOLUTION 3D PRINTING
The sintering technique heats the powdered matter with a laser, which make it possible to have very fine layers, producing high-resolution parts. It is well known that SLS 3D printing produces, in a repeatable way, parts that stand out through their quality, surface finish, and precise details (standard precision = ±0.012 po / ± 0.3 mm). The new printers at Solaxis are equipped with an ultra strong laser and scanner, making the surface finish of the parts very impressive.
GREAT FREEDOM OF DESIGN AND COMPLEX GEOMETRY
Because no support is required during SLS printing, there can be more flexibility in the design and complexity of the parts without impacting their cost. With other 3D printing methods, requiring support materials can increase production costs.
DIVERSITY OF THE MATERIALS AND INNOVATION
The laser sintering printing equipment carefully selected by Solaxis’ engineering team is of the “open” variety. This provides a lot of freedom when it comes to materials and innovation, making it possible to propose the best material for the desired project.
More explicitly, this means that the enterprise is free from the constraints relative to the properties of materials, as the use of the printer is not dependent on the powder supplier. In other words, depending on technical requirements, many innovative materials can be integrated. Presently, the materials used at Solaxis Ingenious Manufacturing for SLS 3D printing are: polypropylene (PP), polyamide nylon 11 (PA11), polyamide nylon 11 carbon-filled (PA11 CF) and polyamide nylon 11 ESD (PA11 ESD).
ADDED-VALUE AUTOMATED POST-TREATMENTS
The company specialized in large-scale industrial 3D printing has (in parallel with the acquisition of SLS printers) acquired automated surface treatment, coloration and sealing equipment, as well as equipment to test and validate different technical properties. Fun fact: following testing, we have noted that post-treatment sealing significantly increases mechanical properties (up to 4X the elongation at break).
With this cutting-edge equipment, the acquisition of testing laboratory equipment and the technical expertise of their team, Solaxis Ingenious Manufacturing can now print superior quality small and medium series parts at a lower cost and in a shorter amount of time. Furthermore, the adoption of an “open” technology gives a glimpse of the development and conception of numerous innovative parts that stand out through their personalized design and specific properties.