Low-Volume Production: Why choose SLS 3D Printing
-
By
Marie-Christine Flibotte
November 27 2023
-
Tech tips and tutorials
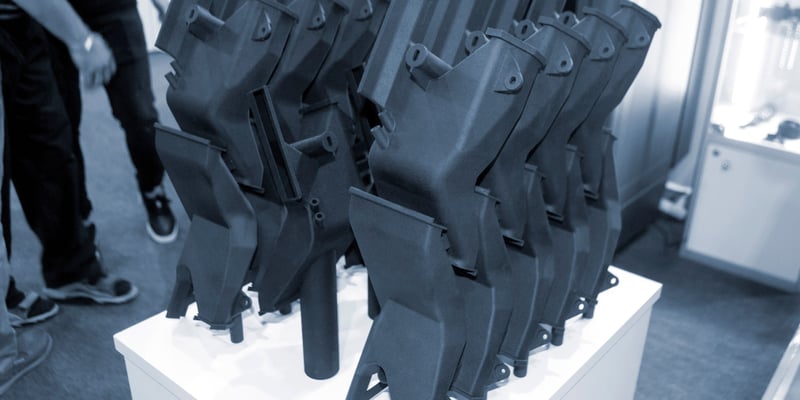
SLS 3D printing and low-volume production are perfectly compatible. In fact, until the emergence of additive manufacturing technologies, thermoplastic parts were produced using the injection molding or forming process. However, these approaches may not be optimal for manufacturing products with complex geometries, and they are even less suitable for customization. The high start-up costs represent a major obstacle in the context of low-volume series production.
Additive manufacturing technologies have evolved significantly and are now used well beyond prototyping. Find out how SLS industrial 3D printing (selective laser sintering) can be the ideal solution for your low-volume series.
Saving Money
It is well known that tooling is a very demanding and expensive portion of manufacturing projects. However, like any additive manufacturing technology, SLS 3D printing does not require the use of molds or specific tooling. SLS 3D printing makes it possible to reduce delays, costs and the necessary labour.
In other words, with 3D printing, there are no setup or start-up costs for your low-volume productions. There is no minimum order quantity, and you don't have to worry about breaking even on starting fees or mold costs, as is the case with traditional manufacturing. This makes 3D printing an effective alternative for your low-volume production.
Now, why does SLS technology stand out among 3D printing technologies for low-volume production? SLS 3D printing is particularly interesting for small and medium volumes since it allows several parts to be produced at once in less time, which optimizes production costs.
Other 3D printing technologies are more limited in this regard. For example, they only allow parts to be produced on the same level, on the platform, while SLS allows several parts to be nested and stacked in the same manufacturing batch.
While injection molding is very expensive for the production of small quantities, 3D production by SLS can easily be optimized for the production of small parts and for orders of less than 1,000 units. Considering all of these advantages of SLS 3D printing, it is a technology of choice for low-volume series productions.
Saving Time
Since SLS 3D printing doesn't require tooling, you don't have to wait weeks or months for molds. You can then quickly launch your production. As soon as the 3D files are received and analyzed, the Solaxis team places the parts in the production schedule and launches them within hours or a few days. In other words, low-volume batch production of 3D-printed parts makes it possible to reduce development cycles and obtain an optimal production rate for small and medium quantities.
Moreover, Solaxis SLS 3D printing equipment offers a remarkable production rate, which can surpass that of standard SLS equipment on the market, thanks to its powerful lasers and scanners. In addition, low-volume production using 3D printing allows for a large production envelope (15 x 15 x 16 inches / 381 x 381 x 406 mm), flexibility and batch optimization.
Fully Functional Parts
If we talk about small series production, we are generally talking about fully functional parts that should be robust and durable. In addition to offering rapid production, other SLS 3D printing advantages include producing strong parts that are ideal for demanding applications.
The components with the materials offered in this technology have excellent mechanical properties and good temperature resistance. By the nature of the process, SLS parts have isotropic properties, which means they are equal in all axes, unlike other 3D printing technologies which generate a weakness in the Z axis. The SLS components are therefore entirely suitable for the production of end-use parts.
Thus, you can easily prototype your model in SLS and use the same solution for your final production. Your prototype will therefore be exactly the same as your final model.
Automated Post-Processing
SLS components in their raw state have a smooth and grainy surface, which can be entirely suited for end-use parts. Moreover, Solaxis SLS 3D printers offer high resolution and high precision of fine details.
It is also possible to use automated dyeing and/or sealing post-processing to maximize the surface finish and obtain a production-quality part similar to an injection part.
The post-processing offered by Solaxis allow a consistently smooth surface finish, as well as quality colouring and repeatable with deep penetration. Our processes are eco-friendly, and since they are automated, they are optimal for small and medium series. Subsequently, the more parts there are, the more profitable the post-processing is and the lower its cost per part.
SLS 3D Printing and Design Flexibility
Parts manufactured in small quantities are often characterized by specific geometries. In other words, they are used for targeted applications or to meet specific needs. SLS 3D printing technology is particularly interesting for complex parts. Unlike other 3D technologies, it does not require support material, so it is possible to overcome the parts' geometric difficulties, without altering their physical and mechanical properties.
This increased freedom of design also facilitates the consolidation of assemblies. By combining several parts into one, it reduces the assembly steps, which can be very advantageous for low-volume production.
Types of parts suitable for small series production using SLS 3D printing
1. Very small parts: Solaxis can print small components very quickly. Easily nestable, we place them among other parts, according to planned production, which means that you receive your orders as quickly as possible.
2. Clips, brackets and fasteners: Nylon 11 is very strong, so it's a great choice of SLS material for your small fasteners and brackets. When producing a product in small quantities, it is difficult to justify spending tens of thousands of dollars on tooling – you may conclude that 3D printing will be the best solution.
3. Custom components: Again, since the process does not require tooling, there are no start-up costs. You can produce unique parts for the same unit price as identical low-volume items.
In short, SLS industrial 3D printing makes it possible to print high-performance parts at a lower cost compared to traditional processes. This major advantage allows you to broaden your range of applications.
At Solaxis, our SLS technology, combined with the size of the manufacturing envelope of our equipment and a nesting (fine fitting) approach, makes it possible to provide 3D printing for low-volume production. We manufacture products in various shapes, whatever the sector of activity, from ground transportation to medical, or even in defence and security, electronics, aerospace or industrial sector.
Do you want to produce complex and high-performance parts in low volumes, in a short period of time and at affordable costs? Contact our team of professionals.