How Additive Manufacturing Can Revolutionize Your Engineering Projects
-
By
Marie-Christine Flibotte
November 17 2022
-
Tech tips and tutorials

Additive manufacturing, or industrial 3D printing, is the production of various types of parts from a digital file, using 3D printing technologies. The process is called additive, because an object is built by adding thin layers of material one on top of the other.
There are great disparities in the 3D printing service offer. This varies from small improvised 3D printing shops set in a garage, to companies specializing in the production of parts using robust additive manufacturing processes of high added value. Applications range from a simple prototype to an end-use part. Learn everything there is to know about additive manufacturing.
Advantages of Additive Manufacturing
Additive manufacturing is a true revolution, because it allows to overcome the limits of traditional methods (machining, molding, injection). It offers new possibilities to create and produce parts more easily, thus offering engineers a great panorama of innovation.
Seeing the ease with which it is possible to obtain a part manufactured by 3D printing, one understands why engineers increasingly integrate it in their projects.
- Use that goes beyond prototyping: robust parts of a quality that allows them to be used directly in production.
- Batch production optimization: parts produced in small quantities at a competitive cost.
- No tools required: eliminates the need to invest in a mold beforehand, and therefore reduces costs and time.
- Flexibility of design: highly efficient technology for parts with complex geometries.
- Consolidation of parts and assemblies: allows combining multiple parts to form a single piece.
- Design iterations and rapid validation of product functionality: quickly experiment with multiple design possibilities without incurring exorbitant production costs.
- Reduced production time: simple and fast process, making it possible to obtain parts in a matter of days.
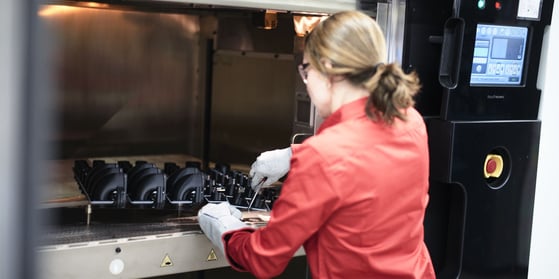
Processes Used in Additive Manufacturing
Among the seven main families of additive manufacturing processes, Solaxis has specialized in two advanced processes in thermoplastics, to produce high-quality parts that are lightweight and robust at the same time. The advanced additive manufacturing service of Solaxis, makes it possible to bring a wide variety of parts and applications to many industries. This recently upgraded service allows us to offer several options in terms of materials, part formats, and production types.
Discover the main families of additive manufacturing processes.
Powder Bed Fusion
The material to be fused is spread in a tank and a laser source moves above it to melt it according to the CAD drawing. Once a layer is fused, the base is lowered and another layer of material is pushed on top. This method makes it possible to produce parts of complex shapes that are very resistant and for which the properties are more isotropic.
Material Extrusion
The material is melted inside a heating nozzle that deposits the hot matter, layer by layer, which bind together as they cool down. This well-known process is the one used by small “desktop” printers, but also by industrial 3D printers with heated chambers. Thus, this method makes it possible to produce a wide variety of standard to high-performance parts. Particularly well suited for industrial production, this process also offers a quality of product sought after in various industries.
Other processes:
-
Directed Energy Deposition
Thin layers of material are fused together using an energy source, such as a plasma arc, laser, or electron beam to melt material which is simultaneously deposited by a nozzle. The DED process can be used to add material to existing components, for repairs or occasionally to build new parts.
- Binder Jetting
Fine layers of powder and binding agents are sprayed alternately. When one layer is complete, the base lowers and the spray head begins the next layer. The common materials used in Binder Jetting are polymers, metals, sand and ceramics, which come in granular form. This process is more practical for the production of decorative objects, toys or models, because the finished product is too fragile for functional parts.
-
Material Jetting
This process is similar to Binder Jetting. With Material Jetting, a printhead (similar to printheads used for standard inkjet printing) dispenses droplets of a photosensitive material which solidifies under ultraviolet (UV) light, building a part layer by layer. The materials used in Material Jetting are thermosetting photopolymers (acrylics) that come in liquid form.
-
Vat Photopolymerization
A liquid photopolymer resin is placed in a vat, which is then solidified using UV rays or a laser. This process requires having supports on the parts. The components produced are generally fragile and the number of compatible materials in this process is limited.
-
Sheet Lamination
Thin sheets of material are bonded using an ultrasonic wave or laser beam welding process. Once the part is finished, the excess material must be removed by cutting or sanding to give it its final shape; this requires more time for production, which is a little less practical for prototyping activities.
Additive manufacturing technologies
Each main family of 3D printing processes is associated with different specific technologies. Under the powder bed fusion operation, Solaxis uses laser sintering technology (SLS) and under the material extrusion technique, we use fused deposition modeling (FDM or FFF).
Selective Laser Sintering (SLS)
Laser sintering is actually a physical reaction that fuses the particles of a powder to form a solid part. It allows the production of complex and high-precision parts. It is especially effective for the production of low-volume production.
Fused Deposition Modeling (FDM/FFF)
The term "fused deposition modeling" (FDM) has been patented by the Stratasys company. The 3D printing technique refers to the deposition of fused material, which is also called Fused Filament Fabrication (FFF). This technology, depending on the type of equipment, is particularly suitable for the production of parts intended for functional applications. Its speed of execution is also ideal for carrying out rapid design checks. In addition, it offers a large choice of materials and colors.
Other technologies available on the market
-
Multi-jet fusion (MJF)
Works on the principle of Powder Bed Fusion, MJF uses an inkjet array and works by depositing fusing and detailing agents in a bed of powder material, then fusing them into a solid layer. The printer dispenses more powder on top of the bed, and the process repeats layer by layer. However, it is difficult to produce parts that have large flat surfaces and the choice of materials is limited.
-
Stereolithography (SLA)
Works on the principle of vat photopolymerization, it employs a reservoir filled with liquid photopolymers, which are solidified using UV light. Printing is quite fast, but requires UV curing time after printing. The parts are in high resolution, but generally more fragile than those made by FDM or SLS.
-
Digital light processing (DLP)
Works on the principle of vat photopolymerization, like SLA, but faster, it uses a projected light source to cure the entire layer at once. The general characteristics are practically the same as SLA. As with vat photopolymerization, the need for cure time makes it a less suitable technology where speed of production is an important factor.
-
Continuous digital light processing and continuous liquid interface production (CDLP and CLIP)
CDLP and CLIP work under the photopolymerization technique, producing the part continuously rather than layer by layer. They were not selected by Solaxis for the same weaknesses as all the technologies related to the vat photopolymerization.
Thermoplastic materials
The materials most used by thermoplastic additive manufacturing technologies fall into three main categories:
Standard thermoplastics
These materials are principally used for the production of parts or prototypes that are not subject to a critical environment. They are inexpensive to produce.
This category of thermoplastic includes, among others: Acrylonitrile butadiene styrene (ABS) and polypropylene (PP).
Engineering thermoplastics
These materials are used in the production of parts that must withstand high temperatures and intense mechanical work.
This category of thermoplastic includes, among others: polycarbonate (PC) and polyamide (PA).
High-performance thermoplastics
These materials are used in the production of parts where strength and predictability are critical. These materials offer very high short and long-term mechanical stability. For example, they combine mechanical properties, thermal and chemical resistance that can meet the highest requirements.
This category of thermoplastic includes among others: PEEK (polyether ether ketone), PEKK (polyetherketoneketone), and PEI (polyetherimide), such as ULTEM.
Typical Applications and Industries that Benefit from Additive Manufacturing
In general, 3D printing applications can be classified into three main categories:
- Single production or low-volume production of end-use parts
- Aesthetic or functional prototypes
- Specialized / custom-made tooling
Clearly, several sectors of activity benefit from the use of a value-added additive manufacturing service.
Aerospace
The polymers and techniques used now make it possible to manufacture flight-certified parts quickly and fully compliant with aerospace standards.
Consumer goods
With the majority of consumer goods being made of plastic, 3D printing proves to be an excellent solution for prototyping thanks to rapid validations and low-volume production.
Defense and security
High-quality additive manufacturing equipment, a high level of cybersecurity and a great engineering expertise, make this service bureau an essential in this field, whether for functional prototypes or end-use parts.
Electronics
Some sophisticated materials with ESD (antistatic) properties are very interesting for applications in this sector of activity, for example where electrostatic discharges are important.
Health
The possibility of producing unique and personalized parts at low cost is undoubtedly one of the great advantages of 3D printing for this industry, whether for orthotics or for parts of medical equipment.
Industrial sectors
All the advantages of additive manufacturing can be a great catalyst for adaptation by producing completely innovative parts in a short time and in a range of materials specifically selected or even developed according to the usage context.
Ground and specialized transportation
Additive manufacturing offers considerable flexibility in part size and material variety. It also streamlines manufacturing, from prototyping and tooling, to the production of spare parts and final parts, thanks to complex, engineering-grade thermoplastic parts.
Do you want to incorporate additive manufacturing into your value chain? Contact us, one of our experts will be happy to help you.