Low-volume Series Production: Application Examples
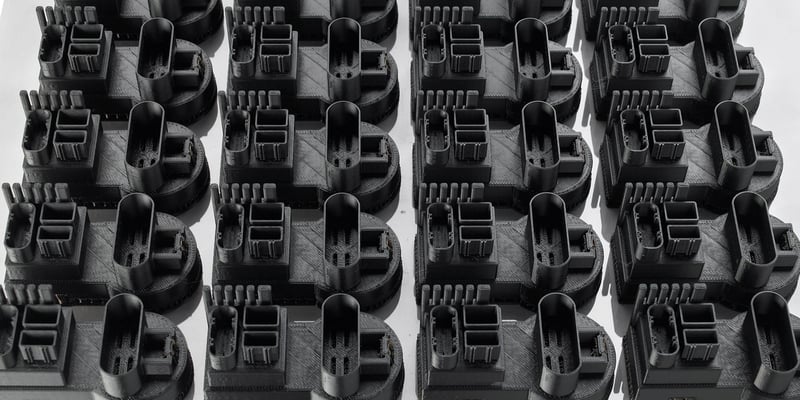
For several years, industrial 3D printing has experienced sustained growth, especially for low-volume series production. Future forecasts are optimistic in every sector of activity. More and more manufacturers use this technology for simple reasons, such as the possibility of designing complex parts beyond prototyping, producing low quantities at a low cost and "on demand" or being able to validate concepts quickly.
Discover, through Solaxis use cases, how additive manufacturing is perfect for low-volume production.
- Examples of Low-Volume Series Manufacturing in the Transport Sector
- Examples of Low-volume Series Manufacturing in the Aeronautics Industry
- Examples of Low-Volume Series Manufacturing in Industrial Sectors
Examples of Low-Volume Series Manufacturing in the Transport Sector
Find out how low-volume series manufacturing can be helpful in the transportation industry.
Electrical Switch Protective Boxes
Industrial 3D printing is the best way to quickly produce batches "on demand" while meeting various technical challenges (complex geometry, robustness, and durability).
Here is a perfect example to illustrate this use in the railway industry. The client needed to design electrical switch boxes for locomotives. Solaxis' additive manufacturing technologies made it possible to address the many challenges of this low-volume production project.
- Short deadlines required to answer security issues quickly: In just 12 working days, the customer received his first batch of 100 parts.
- Low-volume production: The client needed ±100 boxes to start. The investment in tooling was, therefore, not justified.
- Part with complex geometry, cavities, and reinforcements: Because of the part’s odd geometry, machining was not a viable solution financially.
- End-use parts requiring robustness and quality: The solution proposed by Solaxis via industrial 3D printing technologies (SLS printing and deep dye post-processing) combined with a proven material for industrial applications (Nylon PA 11) enabled the customer to obtain durable parts that could be subjected to repeated handling.
Lockout Protectors
Let's look at another example in electric transport, where 3D printing was chosen to manufacture various lockout protectors. The client's objective was to lock access to batteries, fuses, and multiple components involving equipment maintenance risks— connection terminals, battery terminals, etc.
These are the main reasons Solaxis’ additive manufacturing processes were particularly suitable for this project.
- Low-volume production required: The quantity of padlocks is limited because it is related to the number of units to be locked in the factory. The investment in tooling was, therefore, not justified.
- Part with a very uncommon design: There are no existing padlocks for the customer's current units. The design of each lockout part was customized for each unit to be locked.
- Need for nonconductive parts: The durable thermoplastics used make it nonconductive to electricity.
- Easy to locate: The parts were coloured red through our robust and repeatable automated dyeing process to make them easy to find.
- Identification and traceability: The part number was included directly into the design and print process. Identification was needed to indicate the location of the part. The identification is also referenced in the maintenance manual. In addition, it makes it easier to track modifications and revisions of the parts.
Pre-production: Control Panel Protective Covers for Specialized Vehicles
The pre-production stage is the bridge between rapid prototyping and mass production. In this context, low-volume manufacturing by 3D printing finds its whole meaning.
Let's see an example of a pre-production project by Solaxis, which matched the fonctional prototypes with the finished product. The goal was to develop and design covers that protected the control panels of specialized vehicles. The part had many electronic and other component openings, and the customer had to ensure everything was well-positioned. Our industrial 3D printing technologies made it possible to meet the many challenges:
- Design validation: Verify the precision, dimensions, and positioning before manufacturing the mould.
- Simple assembly.
- Pre-production: Around twenty parts were produced for the “beta” phase after the prototyping phase, so our client could deliver a few parts to his customer for final testing. This made it possible to carry out an intensive test phase before more significant volume production. Depending on the results, modifications can easily be made to the part – no moulding or tooling required – or higher-volume production can be started confidently.
- This approach allowed us to print parts for testing while keeping costs down quickly.
Examples of Low-volume Series Manufacturing in the Aeronautics Industry
Discover project examples involving low-volume series manufacturing in the aeronautics industry.
Ventilation Ducts
Low-volume manufacturing lends itself perfectly to the aerospace industry, provided you work with a service provider that holds the necessary certifications. In addition to the repeatability issue, the parts manufactured for this sector present many challenges. Take the case of a project to develop ventilation ducts with complex geometry. Our technologies and expertise allowed us to:
- Use a material that meets FST standards (fire, flame, toxicity), ULTEM 9085 certified grade in this case.
- Design a quality part or even overcome technical issues such as geometry by optimizing the CAD file.
- Improve the durability, performance, or yet again surface properties of the part through post-production stages. For example, a primer-ready finish was applied to seal the ventilation duct. (Not shown in the image).
- Produce “final” parts certified that meet AS 9100, NIAR and FAA standards.
- Manufacture in small quantities (100 units/year) while reducing costs.
- Reduce manufacturing times compared to other methods, such as machining or injection moulding. Industrial 3D printing does not require the production of tooling. Furthermore, the number of components being reduced with the consolidation of parts, the assembly steps are partly eliminated. Of course, these advantages also reduce material or human investments.
Flight Simulator Parts
This concrete example refers to low-volume 3D printing of parts for flight simulators. Indeed, various components intended for this industry can be produced due to the limited production volume and the custom-designed cosmetic parts.
In the case of this particular part, our additive manufacturing technologies, combined with our expertise, have enabled us to address the following challenges:
- Precision required to assemble the parts.
- Repeatability.
- Quality of components, including a finish that meets aerospace standards.
- Rapid production in small quantities according to specific customer needs, with imposed delivery deadlines and multiple release dates to meet their production schedule.
Examples of Low-Volume Series Manufacturing in Industrial Sectors: Complex and Highly Specialized Parts
There are numerous requirements when it comes to designing complex and specialized parts. Take the case of robotic grippers (robotic hands), the perfect example for a low-volume series production (10-100 parts). Here are two concrete examples of projects that we were able to address with our industrial 3D printing technologies.
Robotic Hand for a Production Line: lightness and resistance
The client needed a light and resistant robot hand in order to reduce the payload imposed on the robot during its movements. Our team of experts and our technologies have enabled us to:
- Find a light and robust thermoplastic material facilitating the gripping of parts in the mould, offering design flexibility and ensuring durability. Indeed, if the gripper had been made of metal, it could have damaged the mould.
- Reduce the weight of the part.
- Reduce the number of parts in the assembly (22 components to only 5) and, by side effect, reduce assembly time, as well as improve flexibility in terms of movement or kinematics.
- In this particular case, the printed gripper serves as a buffer. Thus, in the event of a robot malfunction, the gripper will absorb the shock instead of the mould. Its replacement is much less expensive than that of the mould.
Robotic Hand for a Production Line: precision and lack of assembly
The robot hand had to be able to grip the parts in the mould, regardless of their geometry or dimensional restrictions. Additive manufacturing has made it possible to:
- Reduce weight significantly, with a hybrid solution combining aluminum (traditional machining) and thermoplastic (3D printing).
- Combine precision and design freedom to ensure the gripping of parts while overcoming the physical constraints linked to the mould. The gripper generates the suction area (no connection, no suction cup). Parts are sucked in directly by the small, cup-shaped segments.
- Produce an end-of-arm-tooling in a single piece. No assembly was therefore required.
Industrial 3D printing manufacturing of low-volume series is ideal for small quantities, receiving parts on demand, and validating concepts or validating parts with a specific geometric and technical complexity. The possibilities are endless between switch boxes, ventilation ducts, flight simulator components, vehicle interior parts, and robotic grippers. Low-volume series manufacturing, therefore, finds its place in all sectors of activity.
Do you have any questions about low-volume series production? Would you like to validate whether our processes can be adapted to your desired quantity? Our team of experts is here to help.