FDM vs. SLA vs. SLS: Choosing the Right 3D Printing Technology
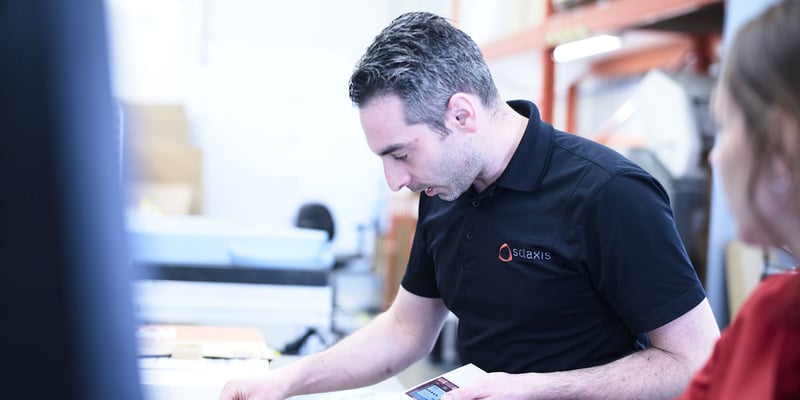
In this guide, we compare the differences between FDM, SLA, and SLS 3D printing technologies to help you reap the many benefits of additive manufacturing, such as flexibility in part design and reduced manufacturing lead times and cost.
Are you considering starting with additive manufacturing but would like to better understand the different available technologies? Get all the necessary information to select the proper process based on your needs, including the estimated time to get the part. From application examples to physical characteristics of the parts, available materials, and production volumes, here’s everything you need to know.
- FDM vs. SLA vs. SLS: Which Technology Should You Choose?
- 5 Factors to Consider When Choosing the Right 3D Printing Technology
FDM vs. SLA vs. SLS: Which Technology Should You Choose?
The design phase is crucial to choose the proper 3D-printing process for a project. At this stage, you can determine the appropriate manufacturing method and evaluate whether 3D printing can be the right choice to meet your objectives. However, other factors also come into play, such as:
- Physical, mechanical, and aesthetic properties of the parts;
- The desired application and function of the part;
- Available materials;
- Production volume;
- Required lead times,
- And cost.
Here is a summary of each 3D printing technology's characteristics.
FDM/FFF |
SLA |
SLS |
|
Technology |
Melting and extruding thermoplastic filaments |
Laser curing of photopolymer resins |
Laser sintering of polymer powders |
Resolution and Precision |
|
|
|
Main Applications |
|
|
|
Materials |
Various ranges of thermoplastic filaments:
|
|
|
Advantages |
|
|
|
Tolerance |
0.012'' |
0.010'' |
0.012'' |
Build Volume Size |
Very large format capability. Large = 100 x 100 x 100 cm |
Medium = 30 x 30 x 30 cm |
Medium = 32 x 16 x 16 cm |
Cost |
$-$$$ |
$ |
$$ |
Minimum Wall Thickness |
* |
*** |
** |
5 Factors to Consider When Choosing the Right 3D Printing Technology
Here’s what you should keep in mind when choosing your 3D printing method.
1- The Process's Manufacturing Capabilities
On top of build volume, there are many factors to consider.
Design Compatibility
The design phase will undoubtedly impact your choice of additive manufacturing technology if this is the manufacturing process you want to go with. It’s important to understand that the choice of process depends on the compatibility of the design with the process itself. Each technology has its particularities, so our specialists work closely with our clients to optimize the design for the selected technology.
Wall Thickness
Verifying the part's minimum wall thickness and assessing the process's limitations are essential. For example, some technologies, such as SLS and SLA, are more suitable than others for printing thin walls.
Geometric Tolerancing
The degree of precision that can be achieved varies depending on the process, geometry and the volume of the parts. Therefore, it's necessary to validate tolerance requirements, as this will impact your choice of 3D printing technology. For example, if the part requires high precision but not enhanced durability, the SLA process could be the ideal choice.
Build Volume
It’s also essential to evaluate whether the build volume size suits the project. Otherwise, you could print the part in smaller sections and assemble it. However, some projects require printing a large part in a single piece. Depending on the processes and equipment types, a wide variety of build volume sizes exist. Since 2010, Solaxis has specialized in large format FDM/FFF printing, and our larger printers can reach up to 1 cubic meter. Additionally, Solaxis equipment provides excellent production stability, reliability, and repeatability for large-format parts.
FDM/FFF technology is generally the best choice when you need to print large parts, since there are more large format offers in the market with filaments printers.
On the other side, SLS 3D printing is an excellent choice for manufacturing smaller parts in small or medium series.
2- Part Characteristics and Functionality
The choice of 3D printing technology depends also on the type of application. Prototypes can be developed to validate geometric or functional concepts, and end-use parts, jigs, or tooling can be manufactured.
Naturally, the requirements vary depending on the type of application. It’s essential to question the parts' characteristics and functionalities: What are the mechanical requirements (chemical resistance, thermal resistance, impact resistance, elongation, biocompatibility, etc.)? How do environmental factors impact durability (humidity, UV)? Does the part need to meet specific standards or norms?
For example, when a part needs to meet high durability and mechanical requirements, depending on the properties and/or standards you want to meet, you are better off choosing SLS or FDM 3D printing. The wide variety of materials and printers with FDM/FFF technology allows for effectively addressing various challenges, from simple validation prototypes to high-performance production parts.
At Solaxis, many of our advanced FDM printers are specially configured to produce parts that meet rigorous aerospace standards.
SLS 3D printing is widely used for the production of end-use parts in short and medium runs. The polyamides used offer an excellent cost-performance ratio.
The SLA process is better suited for printing parts with primarily aesthetic specifications that are not exposed to a critical environment.
3- Materials
Depending on the application and the part's functional requirements, selecting the right material is also crucial. It's essential to analyze available materials compatible with your chosen technology.
FDM 3D printing requires thermoplastic filaments, SLA uses photopolymer resins, and SLS uses polymer powders.
FDM/FFF offers a wide variety of well-known thermoplastics with a proven track record, which makes them easy to use. The range varies from standard to high-performance materials, including ABS, polycarbonate, nylons / polyamides, PEI, PEKK, and thermoplastics reinforced with carbon fibers, etc.
Naturally, higher-end materials require more sophisticated printers and systems. Solaxis uses robust FDM/FFF printers with heated chambers, which allow the reliable use of exotic, high-performance materials distinguished by their excellent mechanical properties.
The material offering for SLS is generally more limited, focusing mainly on PA 12 or PA 11 polyamides. These nylons offer excellent mechanical properties and are highly valued in many applications. SLS-printed parts are also isotropic, making SLS 3D printing particularly interesting for end-use parts.
SLA offers a wide variety of material choices. However, due to the nature of the process, SLA parts are generally less durable over time, regardless of the material, as they tend to become brittle with UV exposure. If aesthetics are more important and the parts are not subjected to a critical environment, you could choose SLA 3D printing with thermosetting materials.
4- Desired Surface Finish
Post-processing is often crucial to achieving the desired surface finish. However, if this can be avoided, you could save time and money. Depending on the desired finish, you could opt for specific technologies.
SLS-printed parts are aesthetic in their raw state, with a smooth finish and excellent resolution for fine details. However, the surface is somewhat granular. FDM/FFF parts are generally rough and show layer lines, which are more or less visible depending on the orientation of the parts during manufacturing.
The SLA process is perfect for smooth, transparent, glossy finishes and plating. FDM can also be used for different types of paint finishes (glossy and matte) and also plating. SLS technology can be used with post-processing treatments such as dyeing and vapor smoothing.
5- Production Rate
Consider your production volume when choosing a technology. A process like SLS printing, where several small parts can be produced quickly in the same batch (nesting), is ideal for small and medium series. This is especially true as a high production pace and deadline adherence directly influence costs.
To summarize, the main factor to consider when choosing a printing process (FDM vs. SLA vs. SLS) is the type of application, which refers to the part's characteristics and functionalities. While FDM and SLS technologies address mechanical challenges, SLA is a better choice when designing parts characterized by their aesthetics. The selection of materials and manufacturing specifics depends on the part's functionality or end-use.
Do you have any questions? At Solaxis, our professionals work closely with clients to optimize designs and select the appropriate 3D-printing process based on their specific requirements.