Applications of 3D Printing in the Defence Sector
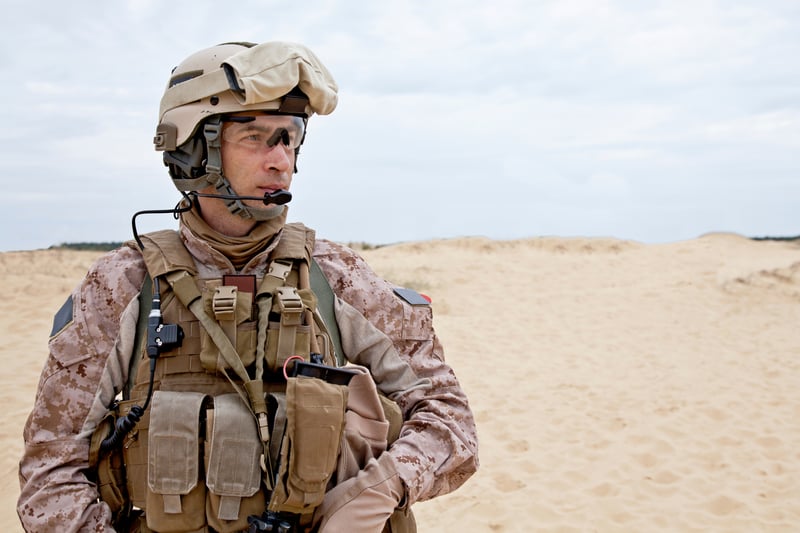
In general, 3D printing allows multiple companies in the defence sector to meet different technical and financial challenges.
In fact, governments worldwide encourage the integration of this technology. This is because, among other things, additive manufacturing offers flexibility, speed, and responsiveness from the prototype to the end-use part.
Discover the benefits of using 3D printing to design thermoplastic parts for the defence sector and its potential applications.
- 3D Printing in the Defence Sector: the Benefits
- When to Use 3D Printing in the Defence Sector?
- The Solaxis Difference: Expertise in 3D-Printing for the Defence Industry
Interested in how we’re shaping the future of defence?
3D Printing in the Defence Sector: the Benefits
In the defence industry, 3D printing is a prime approach for developing and designing complex parts with high mechanical requirements, even with thermoplastics. Here are some examples of how this technology can benefit the defence sector.
Responsiveness and Support for the State's Military Readiness
The “time” factor is of paramount importance in the defence sector. Delivery must be fast, whether designing parts on demand or producing them in small quantities, developing prototypes, or manufacturing tools. This is all the more true given that this sector is highly competitive and that investments on a global scale are substantial for developing parts. Additive manufacturing proves to be an optimal solution to this requirement since it offers flexibility, agility, and speed of implementation. With 3D printing, the final product can be customized without limitations; there can be many iterations, which can be done quickly and easily.
Optimized Supply Chains
In addition to achieving productivity requirements, additive manufacturing simplifies the supply chain. By allowing you to produce on demand without having to invest in tooling, it reduces lead times considerably.
Industrial 3D printing thus offers better inventory management by converting traditional inventory into digital inventory for parts that can be printed on demand. Furthermore, consolidating several parts into one also allows you to reduce the number of suppliers and tooling significantly.
Cost Reduction
Compared to traditional part manufacturing methods in the defence industry, 3D printing can lower overall project costs, depending on the quantities required, because it eliminates the investment in specialized tooling and related costs. It also makes it possible to eliminate certain stages of production, such as assembly, in the case of part consolidation.
Acceleration of Innovation
The defence sector faces many daily challenges, and needs are changing quickly. Additive manufacturing and its ease of implementation make designing new parts with specific and complex physical and/or geometric properties possible. Their functionalities can be tested quickly, whether as a functional prototype or a proof of concept.
When to Use 3D Printing in the Defence Sector?
Considering the benefits of additive manufacturing for the defence sector, multiple applications are possible, whether for producing parts in small quantities, developing prototypes, or designing specialized tools.
Producing Parts in Low-volume Series in the Defence Industry
For some projects in the defence sector, such as aircraft and specialized vehicles, the production volume is certainly lower compared to other areas, such as consumer goods. Hence, 3D printing is perfectly suitable for low-volume production. It can be used to design the following parts:
- Aircraft interior components
- Vehicle interior and exterior components
- Parts for MRO (maintenance, repair, and operations)
- Parts for drones
- Radar components and fibre optics
- Various protective accessories
Development of Prototypes for the Defence Industry
Innovation is essential to the defence sector, so 3D printing is preferred for developing prototypes and validating their physical and mechanical properties. Here are some examples:
- Interior and exterior components of vehicles and aircraft
- The parts for marketing, sales and major presentations
- Substitute parts:
- Awaiting receipt of the original (to achieve a complex assembly, for example).
- To validate the machining program.
- To validate CMM inspection programs.
Specialized Tool Manufacturing for the Defence Sector
Considering the productivity challenges and the responsiveness required in the defence industry, 3D printing is an approach of choice for manufacturing specialized tools such as:
- Tooling for MRO
- Tooling for composite layup/Parts for composite tooling
- Bases for assembly
- Moulds for thermoforming
- Cutting templates
- Brackets and hinges
- Supports and templates for production assistance
The Solaxis Difference: Expertise in 3D-Printing for the Defence Industry
Specializing in industrial 3D printing of thermoplastic parts, Solaxis has all the resources and the structure necessary to meet the requirements and specifications of the defence industry. Our team has developed cutting-edge expertise in this industry, which accounts for a good proportion of our turnover. Here are a few reasons why defence players choose us.
World-class Manufacturing
Solaxis stands out for its team of highly qualified engineers and extensive line of state-of-the-art FDM (fused deposition modelling) and SLS (selective laser sintering) printers. This makes meeting the sector's productivity challenges possible, even for big parts.
Large Format Capacity
The defence industry requires large parts that may need to be produced in one piece. This is the case with vehicle panels, large vehicle consoles, etc. Various customers turn to Solaxis to print large parts in a single piece.
Our large-format units effectively maximize the production area and offer great flexibility in terms of improving production. This optimizes your production time and, therefore, your costs.
- FDM / FFF: The maximum printing area dimension is 40 x 40 x 40 po (1000 x 1000 x 1000 mm).
- SLS: The maximum printing area dimension is 15 x 15 x 16 in. (381 x 381 x 406 mm).
The components can be assembled for parts for which dimensions exceed the size of the production area.
Large Production Capacity
Military contracts sometimes require ensuring a certain production rate in a required time. Solaxis extensive line of printers allows us to meet large volume demands requested in a contract.
- FDM: nine industrial 3D printers, including seven large format ones.
- FFF: two very large format industrial 3D printers and a farm of multiple small 3D printers.
- SLS: two SLS 3D printers, an optimal and efficient process for small parts in low- and medium-volume series.
Engineering and FST (Flame, Smoke, Toxicity) Certified Thermoplastics
It goes without saying that such technologies offer access to a wide choice of materials, from standard thermoplastics (ASA/ABS, PP) to high-performance thermoplastics (PEKK or ULTEM) as well as technical thermoplastics (PC, PA).
FST standards are often required for end-use parts for military aircraft or even certain military vehicles. Solaxis offers various materials that are FST-certified and meet the following standards:
- 14 CFR 25.853
- BSS 7238 and 7239
- AITM 2.0007B and 3.0005
The tests carried out establish that the FST-certified materials at Solaxis meet the requirements of:
- 60s and 12s Vertical Burn
- 15s Horizontal Burn
- Toxic Gas Emission
- Smoke Density
- Heat Release Rate of Cabin Materials
Research and Development: a Highly Equipped Laboratory
Our infrastructures include a highly equipped laboratory (characterization of materials, mechanical tests, dimensional inspection, etc.). This allows us to double-check the part quality, properties, repeatability, and reliability, which are essential requirements in the defence sector.
Efficient Quality Management System
- Controlled production environment according to a precise methodology
- Material traceability - certificate of conformity
- FAI (first article inspection)
- Certifications
- AS 9100:2016
- ISO 9001:2015
- Controlled Goods Program
- Cybersecurity NIST according to CMMC (cybersecurity maturity model certification)
Potential for Industrial and Technological Benefits
For many years, our engineers have used their knowledge, know-how, and expertise to carry out defence, and research and development (R&D) projects. Innovations cover the entire additive manufacturing value chain (materials, processes, quality management, post-treatments, etc.).
Per the ITB (industrial and technological benefits) policy, decision-makers have many advantages when doing business with Solaxis. Indeed, as a Canadian SME with an R&D department, Solaxis meets the program criteria, allowing its customers to benefit from industrial and technological benefits.
Methodologies and Technical Specifications Adapted to the Defence Sector
Thanks to our expertise in 3D printing, certifications, corporate structure, and project-management methodology, Solaxis has been serving the defence sector for several years.
When it comes to more critical and repeatable parts, a precise and detailed quality control methodology is necessary. This is what allows us to certify and control our manufacturing processes to obtain repeatability in production by producing samples during production and checking certain equipment parameters, such as the humidity level, etc.
Do you work in the defence sector and want to innovate, prove a concept, or produce parts in small quantities? Our team of professionals will be happy to advise you!