Technological Diversification: New SLS Technology at Solaxis
-
By
Marie-Christine Flibotte
July 12 2021
-
News and events
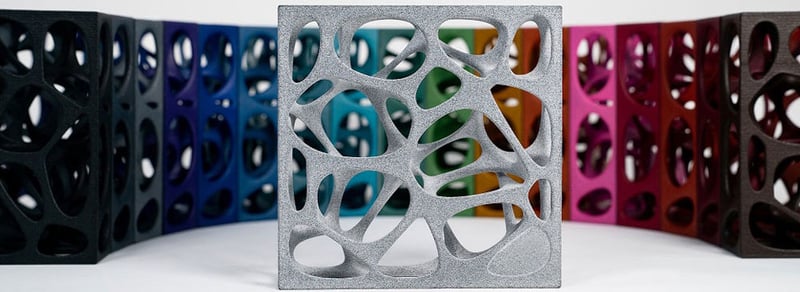
Solaxis Ingenious Manufacturing, leader in additive manufacturing of thermoplastics, invests over 2.39 million dollars in SLS 3D Printing Technology to expand its technological offer and increase its competitiveness in the market.
We are happy to announce a new SLS technology at Solaxis. As specialists in industrial 3D printing of high performance thermoplastic industrial parts, this investment allows us to increase our production capacity, namely through the acquisition of new equipment and cutting-edge digital material.“It is a major project for us. The acquisition of SLS additive manufacturing technologies will increase our monthly production rate 25x, which could reach 5,000 to 20,000 parts per month.” – Francois Guilbault, President of Solaxis.
DIRECT BENEFITS FOR THE INDUSTRIAL SECTOR
A competitive solution for small and medium productions
SLS industrial 3D Printing allows the production of a higher number of parts in less time, which has a major impact on production costs. We are confident we can now better cater to the evolutionary needs of the industrial sector, as well as to their value chain.
There are not enough advantageous technologies available for small and medium productions. Therefore, at Solaxis, we opted for a more competitive 3D printing solution with a higher production throughput, while continuing to provide quality products.
In some cases, SLS thermoplastic powder-based 3D printing technology can even rival traditional manufacturing methods, such as injection. It is perfectly complementary to the FDM (Fused Deposition Modeling) industrial process which has been in place at Solaxis since 2010.
Superior Mechanical Properties
SLS technology allows us to reach superior properties compared to other materials available in the industrial 3D printing market. For example, the elongation at break can reach more than 30% and the ultimate tensile strength is also very high. The isotropic properties (constant properties at every axe) also provide a great advantage compared to filament technology.
A Superior and Automated Surface Finish
The new SLS printers are equipped with an ultra-performant laser, which provides the manufactured parts with a superior finish and a high level of detail.
We also invested in automated surface treatment equipment. The new processes allow the automation of the surface finish and colouring for a smooth, consistent, and repeatable finish. One of the systems allows the production of sealed and washable parts, with a surface similar to injection.
A New R&D Laboratory
Thanks to the new testing equipment, we will be able to parameterize our operation windows, develop our material recipes, and characterize the primary materials and the parts’ performance. This is an aspect that is more and more in demand within large enterprises.
Development of a Decision Support Software
Solaxis is also developing a complex analysis system with different algorithms to accelerate the engineering process, making technical communications with clients more efficient. The ultimate goal is to create a simple, user-friendly online interface to support decision-making. It will be useful for clients who would like to be guided in the selection of their fabrication and finishing options, making technical exchanges with the engineering department easy.
Solaxis’ Objective is Clear: simplifying all small and medium complex parts production projects.
About Solaxis:
Solaxis specializes in large-format 3D printing and small series (1 - 10,000 parts) with advanced and certified thermoplastics, for production parts, functional prototypes and specialized tooling.
Source:
Marie-Christine Flibotte, marketing-communications and inside sales specialist
Solaxis Ingenious Manufacturing
mcflibotte@solaxis.ca
1 877 919-1515 ext. 300