Low-volume Production Methods: Which One Should You Choose?
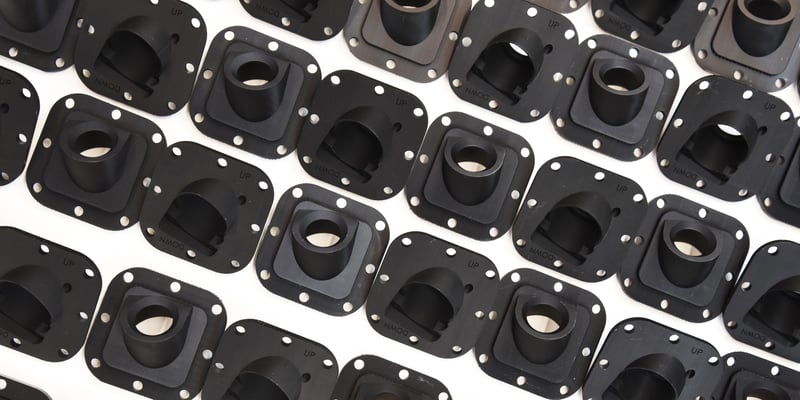
Low-volume production methods all have their advantages and disadvantages. When companies need to validate the characteristics of a part before its large-scale manufacture, or when demand is low, they usually opt for either CNC machining, injection moulding, or additive manufacturing.
Find out which low-volume manufacturing method best suits your needs.
1. CNC Machining
2. Injection moulding
3. Additive manufacturing
1. Low-volume Production Method: CNC Machining
Computer numerical control (CNC) machining is an automated manufacturing method known as “subtractive”. This means that the part is created from a block of polymer, for example, from which material has been removed. Different machining strategies can be adopted such as drilling, milling, or turning.
CNC machining lends itself perfectly to low-volume production because it makes it possible to quickly manufacture parts of excellent quality, regardless of their size. Although the machining operation takes place at high speed, the preparation steps can be long and require the intervention of a large number of professionals. This can therefore have an impact on costs. It is all the more true that this manufacturing method not only requires specialized tools, but also generates material losses.
|
CNC Machining |
Advantages |
|
Disadvantages |
|
2. Low-volume Production Method: Injection Moulding
To manufacture a part using the injection moulding method, the first step is to melt the plastic. In a second step, the material is injected into a mould and then, following the cooling stage during which the part is solidified, it is extracted.
When it comes to validating certain mechanical or physical characteristics of parts, injection moulding can also find its place in the production of low-volume series. Of course, the ultimate goal is high-volume manufacturing. Indeed, although this approach gives the parts precision, resistance, and durability, we cannot dismiss that the design of the mould is long and expensive, not to mention that specialized tooling may be required. However, we can opt for low volume injection molds, which are more economical.
|
Injection Moulding |
Advantages |
|
Disadvantages |
|
3. Low-volume Production Method: Additive Manufacturing
Additive manufacturing, also called 3D printing, consists of manufacturing parts by adding material in successive layers, from a CAD file. The high manufacturing speed and the great flexibility, in terms of part design, make it a method of choice for low-volume production, especially with SLS 3D printing. Indeed, the advantages of additive manufacturing are highly significant when it comes to validating a concept, analyzing certain properties of parts and even starting production. In addition, 3D printing does not require the involvement of a large number of operators (little or no assembly), does not require tools/moulds and generates very little waste.
This approach is therefore economical for certain types of projects, and medium- to low-volume series. The downside? Additive manufacturing has limitations when it comes to the part dimension. Furthermore, depending on the specifics of the parts to be manufactured, subtractive methods can be favoured to achieve the requirements in terms of tolerance compared to the additive process.
|
Additive Manufacturing |
Advantages |
|
Disadvantages |
|
At Solaxis, our team of engineers masters 3D printing technologies, but they also have knowledge of different manufacturing methods that lend themselves to low-volume series production. Indeed, before undertaking any new development, we carry out an in-depth analysis of the aesthetic, physical, and functional requirements of the parts in order to determine the approach that will be best suited to their manufacture. We have the interests of our customers at heart, so we will not hesitate to refer you to CNC machining or injection moulding if these methods prove to be a better choice.