Additive manufacturing (or industrial 3D printing) is a fast-growing, innovative and revolutionary technology. However, few companies are aware of its full potential and many positive impacts.
As we will see in this series of articles, it consists of much more than just a prototyping tool. Additive manufacturing comprehensively integrates into a company’s value chain, with benefits in a variety of areas, from product development to design, innovation, engineering, manufacturing, supplies and more.
In these four articles, we offer avenues to help you spot improvement opportunities for your production line thanks to this leading-edge technology. This first article suggests tips and tricks for cutting down on lead and production times, mainly related to design validation and prototyping.
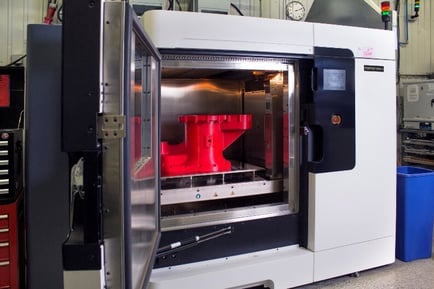
- DETERMINE WHERE YOU WOULD BENEFIT FROM SHORTER LEAD TIMES.
- Because 3D printed parts require no molding or tooling, you enjoy lower costs and timeframes compared to the traditional methods.
- The technology provides you with parts “on demand,” regardless of their shape, complexity or dimensional volume (depending on the 3D printing technology).
- During design validation, additive manufacturing allows you to easily and simultaneously test out different ideas and concepts—so you can quickly get a maximum of perspectives before moving forward with a project.
- ESTIMATE HOW MUCH EACH ADDITIONAL DAY OF LEAD TIME COSTS YOU.
- The 3D printing approach is fast and easy, even for complex geometries, so you can be sure of meeting your production deadlines and avoiding added expenses.
- Thanks to faster manufacturing, you can make a substitution part while waiting to receive the original one. This means you can continue your project and validate assemblies, in turn avoiding lateness and delays.
- EVALUATE HOW DETECTING AND CORRECTING ERRORS AT THE BEGINNING OF THE DESIGN PROCESS WOULD SHORTEN YOUR PRODUCTION TIMEFRAMES AND BOOST YOUR PROFITABILITY.
- During the design stage, a printed prototype enables you to validate geometry, ergonomics and design. The prototype mimics the actual product, allowing you to test the part and make any necessary modifications before beginning production.
- Depending on the 3D printing technology you choose, the object may be subjected to stringent tests to finalize proof of concept and validate technical parameters in a context of actual use. Thanks to the functional prototype, you can test technical risks, and identify defects faster than with simple digital modelling.
- Validating your design upstream before going into production gives you the assurance that the end product will be functional and that your project will be a complete success. You will also be able to avoid costs associated with design errors that are realized too late.
Have a project in mind? Have questions about the feasibility of a 3D printing project? Wondering if your design is optimal for 3D printing?
CONTACT OUR EXPERTS!
Established in 2010, Solaxis has developed a unique approach that makes for absolute best results. We tap into our unrivalled expertise to make sure all the parts we produce are optimized and perfectly match your priorities, including specific technical requirements, functionality, surface finish, assembly and weight. We support our customers in optimally designing their parts for 3D printing.
Next article: