Design Tips for SLS 3D Printing
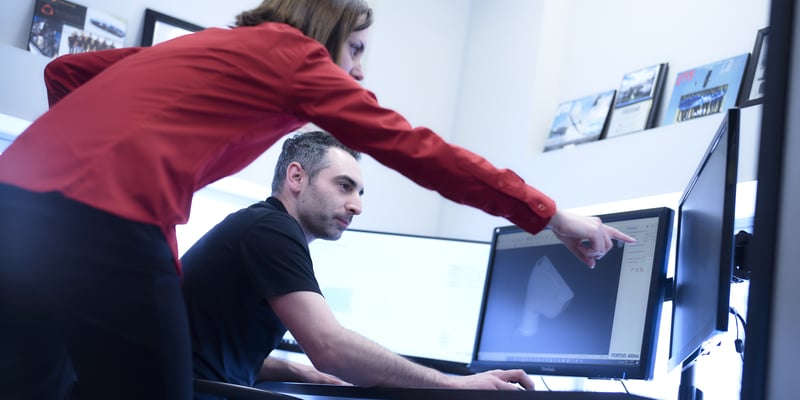
Following design tips for SLS 3D printing (Selective Laser Sintering) will allow you to manufacture parts that stand out for their geometric complexity as well as their mechanical properties. Indeed, SLS additive manufacturing is a technology of choice for designing quality industrial parts.
There are some design rules for SLS 3D printing to optimize the physical characteristics and aesthetics of the parts, and to ensure the success of your SLS project. Here are the main ones.
Dimensions of the Maximum Printing Area
Standard Precision
Wall Thickness
Hollow
Holes and Channels
Engraved and Embossed Details
Dimensional Considerations
To ensure the quality of parts manufactured by SLS 3D printing, it is essential to know and respect certain dimensional rules.
Dimensions of the Maximum Printing Area
The size of the printing area can vary a lot from one printer to another. Make sure to enquire about the dimensional limits of the equipment you or your partner is working with, to know their limits.
SLS equipment used at Solaxis can produce parts up to 15 x 15 x 16 in. (381 x 381 x 406 mm) in size. It is also possible to use assembly techniques to produce larger parts.
Standard Precision
Tolerances in SLS 3D printing are +/- 0.3 mm. It is important to know that the larger the size of the part, the more this number increases.
Thermoplastic parts manufactured by SLS 3D printing may be subject to certain deformations depending on their geometry. A thorough analysis of the drawings allows for adjusting measurements to meet standard dimensional requirements. Additionally, there are some alternatives to limit distortion, such as adding support ribs under flat surfaces. If your project requires tight tolerances, be sure to identify critical areas on your 2D files and discuss them with your specialist to validate the proposed solutions.
Wall Thickness
Wall thickness is the measure between the exterior and interior surfaces of a part. The required mechanical requirements can have an impact on the choice of wall thickness. Thicker parts bring more resistance, while thinner ones bring more flexibility. However, certain restrictions must be considered to prevent the part from collapsing during printing or breaking during post-processing. These can vary depending on the materials. Generally, SLS 3D printing requires a minimum wall thickness of 1 mm for the majority of materials, for example, PA11. However, for polyamides reinforced with carbon fiber, it is more like 2 mm.
For wall thicknesses that fall below the guidelines, it is possible to integrate supports or hinges to prevent deterioration or breakage.
Considerations for Certain Configurations
To achieve the physical requirements or to design some characteristics of a part that will be 3D-printed with SLS technology, certain strategies must be put in place. These are accompanied by design rules for SLS 3D printing that must be respected to achieve the desired quality.
Hollow
By the nature of the process and the effects of the heat generated during printing, it is preferable to hollow out the parts in certain cases, or to design unfilled parts. You can discuss this in more detail with your specialist. Printing hollow parts makes it possible to reduce the weight of the part or to limit its deformation. It will be necessary to add one or more exhaust holes to the component if you wish to evacuate the unsintered powder trapped in the part.
The temperature required during SLS 3D printing can cause the powder to melt near the exhaust hole or holes. These can then become blocked. To avoid this phenomenon, their diameter must be greater than 3.5 mm.
Holes and Channels
Along the same lines, depending on the aesthetic requirements or functionality of the part, the design may require holes or channels. In such instances, the minimum diameters required will be 1.5 mm and 3 mm, respectively.
Engraved and Embossed Details
SLS additive manufacturing allows you to print text, engravings, or raised elements. However, a certain height or depth is required so that these patterns are not rubbed out during printing or post-processing.
For example, to ensure the visibility of a text, its minimum size must be more than 2 mm. We also recommend using a sans serif font. For engraved or embossed motifs, the minimum depth or height must be 1 mm.
Multiple Applications
At Solaxis, we print thermoplastic parts by SLS for different sectors such as:
- Electronics (housings, covers)
- Health and medical (orthoses, casings)
- Automotive and specialized transportation (interior and exterior parts, tanks, and other systems)
- Industrial (fans, jigs and fixtures, tooling)
- Defence and security (military vehicle components)
- Aeronautics (various certified aircraft interior parts)
Our experts' knowledge and know-how helped determine these SLS 3D printing design rules aimed at maximizing the efficiency of manufactured parts through SLS 3D printing. We thus ensure that we achieve optimal quality, whether it is developing a prototype, validating a proof of concept, or producing in small or medium series.
Questions about SLS 3D printing? Our team will be happy to assist you! Contact us.