Applications of SLS 3D Printing in the Electronics Industry
-
By
Marie-Christine Flibotte
April 9 2025
-
Applications industrielles
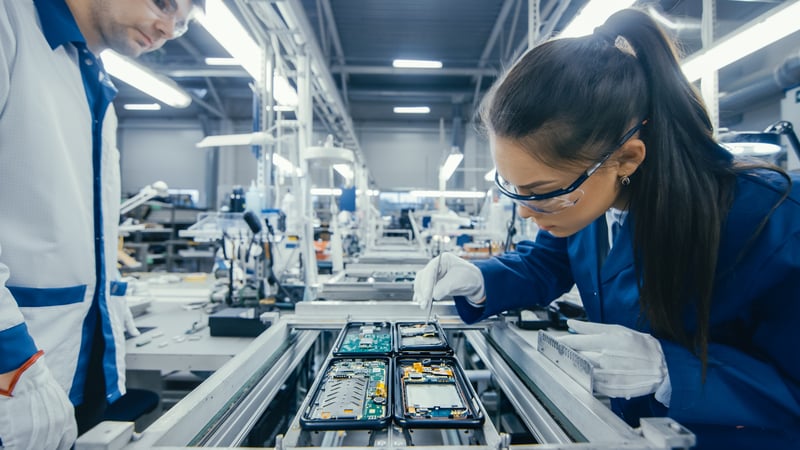
For some years now, SLS technology has been widely used in various sectors, due to the advantages and specificities that it confers. And the electronics industry is no exception. Let’s take a closer look at the benefits and potential applications of SLS 3D printing in electronics.
The Benefits of Industrial SLS 3D Printing for Manufacturing Electronic Components
Flexibility
SLS technology does not require supports, which means that no structure is required to hold the part while it is taking shape. This results in great flexibility for designing parts. This is a significant advantage for the electronics sector, since SLS technology makes it possible to develop and print personalized parts that perfectly match the shape of its various components (for example protective casings).
Complex Geometries
The new design possibilities and the level of flexibility offered by SLS 3D printing provide the capacity to develop complex geometries that are impossible to achieve with other traditional manufacturing techniques.
In a context where mass customization is increasingly important, this flexibility can certainly allow electronic companies to increase their competitiveness.
Limit Electrostatic Discharges with the PA11 ESD
One of the main challenges for manufacturers of electronic components is to limit electrostatic discharge (ESD). The latter can occur when two electrically charged parts come into contact, among other things. This can then result in the deterioration of the electronic components, if not more serious damage (fire, explosion, etc.).
In order to limit any risk related to electrostatic discharges, using the SLS 3D printing of PA11 ESD nylon enclosures is an interesting avenue. In addition to its electrostatic dissipation characteristics or its low resistivity, at Solaxis we turn to this material to develop and manufacture parts requiring certain mechanical properties such as tensile strength and high elongation.
Increase in Productivity
Due to its specificities (size of the manufacturing envelope, nesting technique), SLS 3D printing makes it possible to produce many small parts in short lead times and even meet productivity challenges (orders of up to 10,000 parts per month).
No Assembly Process
With SLS technology, it is possible to consolidate assemblies by printing multiple parts as a single piece, thereby eliminating the need for any assembly operation!
Optimized Supply Management
With SLS, inventory management and, implicitly, supply chain management, are more efficient because it is possible to order parts on demand, meaning there is no need to keep an inventory, only when the need arises. There is no minimum quantity required to start a cost-effective production.
Additionally, the amount of material required to manufacture parts using SLS 3D printing can be significantly lower than that used in traditional processes.
From Replacement Parts to Low-volume Series Production: A Simple and Fast Production Process
The benefits generated by SLS 3D printing such as flexibility, the possibility of designing parts with complex geometries, the use of PA11 ESD, and the speed of production make it possible to produce low-volume series, to print products in limited editions, or to manufacture replacement parts. In other words, opting for SLS technology makes it possible to overcome the burden of the minimum number of unit requirement.
SLS 3D Printing and Custom Casings
At Solaxis, we are frequently called upon to produce casings for the electronics industry. These custom enclosures provide both protection and thermal dissipation for electronic components. The design can be tailored to specific needs for devices such as sensors, electronic boards, or wearable devices. These parts are characterized by their quality or yet again their precision in detail as well as their solidity. Consequently: these custom enclosures are perfectly suited to the electronic components they house! Did you know that we can also add various functionalities to these casings depending on your needs?
SLS 3D Printing and Custom Brackets
Other applications are also popular, such as custom brackets and fixtures for printed circuit boards (PCBs). Custom supports for holding PCBs in electronic devices can be easily made using SLS. These parts can be designed to precisely fit the shape and size of the boards, providing stable mounting while being lightweight and durable.
SLS 3D Printing and Complex Internal Components
SLS 3D printing enables the production of complex internal components, such as heat sinks or integrated cable guides, which are difficult to manufacture with traditional methods. These parts can be designed to optimize thermal performance and improve cable management in compact electronic devices.
In conclusion, whether for a single prototype or a few thousand parts, SLS 3D printing is a technology of choice for the field of electronics. Some printing materials, offered by Solaxis, make it possible to counter the issue of electrostatic discharges in this sector, to design casings and various electronic components, regardless of the geometric complexity of their components. Finally, opting for 3D printing makes it possible to overcome current supply problems while remaining respectful of the environment.
Questions about the applications of SLS technology? Contact our team of professionals today!