Everything You Should Know About High-Resolution SLS 3D Printing
-
By
Marie-Christine Flibotte
August 17 2023
-
Tech tips and tutorials
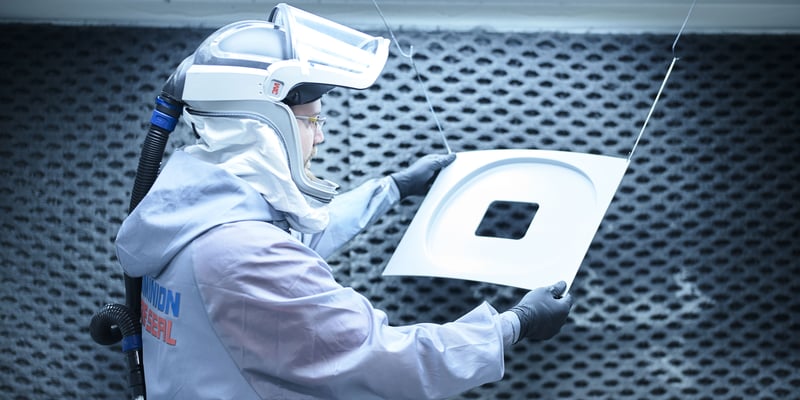
As you may know, SLS 3D printing is a powder bed fusion method, which uses a laser beam to locally sinter the polymer powder, while manufacturing the parts layer by layer. SLS 3D printing has many advantages both technically and industrially, this technology is increasingly used in many areas. Whether you are looking to optimize your internal production processes, or you want to evaluate SLS technology for your engineering project, find out everything you need to know about high-resolution SLS 3D printing.
Advantages of SLS 3D printing
As mentionned, SLS 3D printing presents many advantages. SLS 3D printers are characterized by their heat source, the type of laser used, and the specificities of the powder distribution and deposition systems.
Solaxis has acquired industrial-grade and large-format equipment to sustain its position as a world-class manufacturer. The Solaxis SLS printers are equipped with an ultra-powerful laser and scanner, offering a superior surface finish and better binding between layers to maximize the mechanical properties, which was demonstrated by various mechanical tests. Here are the main advantages of SLS additive manufacturing at Solaxis.
Cost Optimization
SLS 3D printing offers a nesting approach, which maximizes the number of parts produced in the same production batch. This makes it possible to optimize the productivity of the projects, by reducing the production times and the costs of the parts manufactured in series-type production.
High Productivity and Throughput
The nesting approach combined with the size of the manufacturing frame (15 x 15 x 17 inches) of our equipment allows the production of low- and medium-volume orders of up to 20,000 parts per months, for example interior parts of vehicles, orthotics, various casings, components of industrial and medical equipment...
Part Durability
The SLS technology achieves superior properties compared to other processes in the industrial 3D printing market. With this powder fusion process, the properties are isotropic, that is to say equal in all axes, which makes it possible to obtain high quality and more durable parts.
High-Resolution Printing
As our SLS 3D printers are equipped with an ultra-powerful laser and scanner, the parts produced stand out for their quality, surface finish and precision (standard precision = ±0.012 in./±0.3 mm).
Great Freedom of Design and Complex Geometry
Since SLS printing requires no supports, this technology offers more design flexibility, making it an excellent technology for producing complex parts and/or consolidating assemblies.
Material Diversity
The laser sintering printing equipment used by Solaxis is of the “open” types. This leaves room for great freedom in terms of innovation and material diversity that can be integrated.
FDM, SLA, and SLS: What is the difference?
In recent years, SLS 3D printing technology has been selected for its high productivity, particularly for the design of prototypes and the production of parts of low- and medium-volume series. This makes it very competitive with regard to other additive manufacturing processes such as stereolithography (SLA) or fused deposition modeling (FDM).
Comparison: FDM, SLA, and SLS
These three technologies differ essentially in the specificities of thermoplastics, the advantages they hold, and the properties of the parts produced. This is what you should remember:
|
FDM |
SLA |
SLS |
Materials used |
Thermoplastic filament |
Photopolymer resin |
Polymer powder |
Advantages |
Large format. Diversity of materials. Relatively low cost. |
High resolution and precision, finesse of details. Wide choice of materials. |
High productivity. Relatively low cost per part. No supports required. |
Part properties |
Variable according to material and production equipment. |
Usually more fragile parts. |
Excellent mechanical properties. Isotropic properties. |
Applications |
Proof of concept, functional prototype and end-use parts. |
Aesthetic prototype, molds and tooling. |
Functional prototype, proof of concept, short series production parts. |
Materials Compatible with SLS 3D Printing
SLS 3D printing is compatible with different types of materials. At Solaxis, we currently prioritize:
- Nylon 11 - PA 11
- Nylon 11 ESD – PA 11 ESD
- Polypropylene - PP
Nylon 12 is a widely used material by the community when it comes to SLS printing: It makes it possible to manufacture quality parts. However, at Solaxis, we opt for Nylon 11 (a material very similar to Nylon 12), since Nylon 11 produces parts of better quality with clearly superior mechanical properties: high elongation at break, impact resistance, tensile strength, isotropy of properties.
|
PP |
PA 11 |
PA 11 CF |
PA 11 ESD |
Characteristics |
- Excellent chemical resistance - Relatively high ductility - High rigidity - High elongation at break (30%) - Low moisture absorption - Relatively low cost
|
- Robust and rigid - Impact resistance - Elasticity - High elongation at break (45%) - Biocompatibility
|
- Tensile strength - Temperature of deflection under load of 189 °C at 0.45 MPa - High strength to weight ratio
|
- Low electrical resistivity - Electrostatic discharge behavior
|
Applications
|
- Industrial equipment and tools -Reservoirs / tanks - Cleaning tools |
- Orthotics |
- Packaging line tooling - Assembly jigs |
- Electronic cabinets - Casings and tooling for the electronics sector |
Therefore, the choice of material goes hand in hand with the type of application and implicitly the required mechanical properties.
SLS 3D Printing: Applications
SLS 3D printing can be used for several types of applications. These are some of the main ones.
Production: Low-volume Series and Complex Parts
SLS 3D printing does not require support and makes it possible to design parts with a certain amount of geometric complexity. Moreover, the nesting approach combined with the size of the manufacturing envelope (15 x 15 x 17 inches) of our equipment allows the production of low-volume series or of quite substantial volumes, and at good prices.
Product Development: Prototyping
SLS additive manufacturing offers great design freedom, overcomes certain geometric difficulties and offers short lead times. It is therefore an excellent alternative for developing functional prototypes and proofs of concept. This allows evaluation of the model (fit, form and function), technical design, mechanical properties, and part performance (for example, wind tunnel testing).
This approach is already adopted in several sectors of activity. SLS 3D printing not only validates a functional part through testing, it also reduces the risks associated with product development. In the end, you save time and money.
- Models for design validation (fit, form and function)
- Performance testing and filed testing
- Technical design validation
- Wind tunnel test models
- Etc.
Tooling and Patterns
SLS printing is capable of very high precision when it comes to part details. For example, it is possible to manufacture parts with thin walls, without affecting their mechanical properties (strength, durability). This technology lends itself very well to industrial applications such as:
- Rapid tooling manufacturing (concept development and transition tooling),
- Inserts of injection moulding,
- Visual tools for tooling and manufacturing,
- Precision moulding patterns,
- Jigs and fixtures,
- Casting moulds (sand casting),
- Etc.
Optimizing Designs for SLS
SLS parts do not require supports, which makes it one of the 3D printing technologies allowing the greatest design freedom.
SLS 3D printing can actually produce many functional features on the parts. Combined with the range of technical polyamides available from Solaxis, this makes this SLS technology perfectly optimal for end-use parts.
Here are some recommendations to consider when designing:
Minimum wall thickness |
0.8 mm-2.0 mm, depending on material |
Hole diameter |
1.5 mm minimum |
Drainage/discharge hole diameter |
3.5 mm minimum |
Text height |
2 mm minimum |
Size of specific small features (for example, pins) |
0.8 mm minimum |
Relief height |
Higher than 1 mm |
Engraving depth |
Deeper than 1 mm |
Standard precision |
±0.3 mm or ±0.5 mm, whichever is greater |
Solaxis, Your Partner of Choice for SLS 3D Printing
At Solaxis, we have chosen our SLS equipment wisely, in order to remain a world-class manufacturer. Our SLS printers are equipped with a high-powered laser and scanner, which increases the surface finish of the parts produced and the mechanical properties of the parts.
“Open” Manufacturing Technology and Innovation
Our SLS printers are distinguished by their called “open” manufacturing technology, allowing great freedom in the choice of materials and design. In addition, the particularities and diversity of laser beams (fiber optics, CO2) also make them world-class grade equipment.
To be more explanatory, this means that the characteristics of this "open" 3D printing equipment, allow us to free ourselves from the constraints relating to the properties of the materials, since the use of the printer does not depend on the powder supplier.
Therefore, depending on the mechanical requirements, the geometric complexity of the parts including their dimensions and the sectors of activity, several materials can be used at Solaxis:
Our experts are available to support you and advise you on the best material to use for your project.
SLS technology is a technology of choice when it comes to 3D printing thermoplastics:
- Cost competitiveness with regard to other thermoplastic 3D printing technologies
- Rapid manufacturing of parts with complex geometry
- Flexibility in terms of materials and production volume (prototype, small series, production)
All of these advantages make it possible to envision the adoption of this technology in a wide range of sectors. For example, at Solaxis, we use this technology in sectors such as aerospace, electronics, health and medical, ground transportation, defence and security, consumer products and for industrial applications.
You have a project in mind? Contact us, our experts will be happy to help you.